Marine Applications of Carbon-Core Materials
Polypropylene is a thermoplastic polymer with visco-elastic properties. Bee-developed honeycomb in hexagonal form is one of the most efficient structures found in nature.
Using complex processing techniques, a proprietary co-polymer compound of polypropylene can be formed into honeycomb panel stock, resulting in a structure with exceptional specific rigidity (stiffness to weight) and energy absorption, while incorporating the material benefits of visco-elasticity. Composite sandwich panel constructions using CarbonCore Plastic Honeycomb are the realization of this DYNAMIC IMPACT RESISTANCE TECHNOLOGY.
Honeycombs can be constructed with many different materials. The most common method of fabrication is adhesive bonding flat sheets of material with offset lines of adhesive, and subsequently expanding them to open the cells. This technique is commonly used to used fabricate honeycomb from paper or aluminum products. By contrast, honeycombs may be constructed from thermoplastic materials by extruding profiles through a die and then joining them by thermal fusion to form large blocks, which eliminates the need for adhesives. Regardless of the method used, sheet stock can be cut from the large blocks of honeycomb in the same fashion as foam or end-grain balsa. However, the sheet stock cut from the extruded profiles will possess mechanical properties in the longitudinal and transverse directions of the core that differ from the properties of adhesively bonded and expanded honeycombs. Extruded honeycombs, such as CarbonCore Plastic Honeycomb, have equal properties in either axis.
Although the use of sandwich construction in marine applications often has been the subject of debate, the problems that stimulate the debates are typically traceable to early boat designs that employed inadequate building methods or specified the wrong core material for the engineered load. These isolated incidents, however, are not the norm. The great majority of sandwich-constructed boats have performed well over the years.
Why is honeycomb sandwich panel construction used?
The primary reason is to maximize the mechanical efficiency of structures to save weight and raw materials. Sandwich panels mimic the characteristics of an I-beam, using flanges to support tensile and compression loads, with a shear web joining the flanges. Composite skins constitute the flange portions of the I-beam. Instead of using narrow webs, as is done on the centerline of an I-beam, low-density core materials are used throughout the space between two skins. The schematic on the right demonstrates the effectiveness of a honeycomb panel (Al) compared to a solid aluminum sheet in 1/4-inch thickness. By using a core material to double the thickness, the flexural stiffness is increased seven (7) times at almost the same weight! The mechanical efficiency of this cored sandwich can be dramatically increased by increasing core THICKNESS.
Core materials have one or more intrinsic properties that are advantageous for specific applications, and these properties must be carefully considered when designing composite structures. Just as composite laminates have specific properties determined by the selected reinforcements and matrix resins, sandwich panels take on many additional characteristics that are uniquely determined by the selected core material. Distinguishing materials by their respective limitations, including strain-to-failure, is as important for core as it is for fibers and resins. Elasticity has been an essential issue in the debate concerning the risks of introducing brittle fibers like carbon, or opting for the damage tolerance provided by aramid fibers, such as Kevlar. When it comes to core material, it is also helpful to compare characteristics in relation to elasticity and damage tolerance. Of the commonly used core materials, balsa and aluminum honeycomb are among the least elastic. Polymeric foams demonstrate a wide range of properties, depending on their specific formulations and densities. In general, thermoset polymers are less elastic than thermoplastics. Urethane-based foams are thermoset, and are the least elastic of the polymeric foams. PVC foams demonstrate a wide range of elasticity, from blended “cross-linked” foams to “linear” foams. Of the foam types commonly used, SAN (Styrene-AcryloNitrile) Foams are the most forgiving, but cost is at a premium. It also is common in foams for the temperature resistance to decrease when their elasticity is increased.
This is DYNAMIC IMPACT RESISTANCE TECHNOLOGY. This is CarbonCore.
By comparison, CarbonCore thermoplastic honeycombs (or DYNAMIC IMPACT RESISTANCE TECHNOLOGY) have elasticity in the 200 percent range! In real-life terms, the better the elasticity, the greater the IMPACT STRENGTH and derived TOUGHNESS.
Or, in reverse comparison, the stiffer the core material, the better it transfers impact and vibration energy from the side of the impact (or outside skin) to the inside skin, thus subjecting the inside skin to face buckling, delamination or catastrophic failure.
The basic design criterion for DYNAMIC IMPACT RESISTANCE TECHNOLOGY is damage tolerance – a measure of the panel’s retention of its structural properties after damage compared with its undamaged properties. It is considered desirable for core to deform elastically yet remain intact with the facings. This enables a panel to support a considerable percentage of its designed dynamic loads, despite the damage. In theory, this property can be advantageous when parts are designed to be “under-built,” that is, they have the damage tolerance calculated into the part itself, thus saving weight and cost.
Another important design aspect of DYNAMIC IMPACT RESISTANCE TECHNOLOGY is its ability to dampen sound and aid in quieting the structure.
One must not confuse the two acoustical phenomena: sound transmission loss and sound absorption.
Sound transmission loss relates to the use of sandwich panel as a sound barrier, in which case elastic honeycomb core is not very effective in higher frequencies, although it is extremely effective in lower frequencies. (In the 125 to 150 Hz range of structure-borne vibrations.) Another great plus for all honeycomb sandwiches is great fatigue resistance and toughness. By nature of its design, a honeycomb’s cells form thousands of small webs inside the panel, which means that failure of a web (or even a series of webs) does not inevitably lead to catastrophic failure of the whole panel.
The criteria for sound transmission loss is high weight and low flexural stiffness (just the opposite of DYNAMIC IMPACT RESISTANCE TECHNOLOGY), which is why lead is an effective sound barrier. The visco-elastic nature of the plastic honeycomb technology effectively cancels out the sound and vibration energy in a given frequency range. It also is aided by the shape of the honeycomb cell, where sound waves bounce from cell wall to cell wall and get further absorbed by the visco-elastic nature of the plastic.
It should be understood that not all thermoplastics are viscoelastic.
Polypropylene, which is used in Carbon-Core Plastic Honeycomb, is visco-elastic and gives its unique properties of impact resistance, resilience and sound damping. The hexagonal cell form provides the compressive strength that separates the two skins to maintain panel stiffness. Impact loads are dissipated by the elastic and damped response of the core under the skin – a controlled deflection with recovery. This equates to the spring-and-shock-absorber system used in automotive suspension. Without the damping component, the structure would respond like a spring and have resonance. Damping indicates an energy conversion, or hysteresis. The “Law of the Conservation of Energy” states that energy cannot be created or destroyed; however, you can convert the energy to another form. In this case the kinetic energy of the impact is converted into small amounts of heat as the viscous nature of the polypropylene provides resistance to deflection, as well as to recovery. The damped resilience permits the use of lower safety factors in designing structures because they are less prone to catastrophic failure. Other core materials, such as balsa and rigid foams, will be initially stiffer, stiff enough to tempt a designer to use thinner laminates. While they may be more rigid, that very rigidity makes them prone to catastrophic failure under impact because there is no damping or shock absorption. Failure modes in balsa-cored panels include contra-coup de-lamination where a plug of end-grain balsa is dislodged under the impact point, which pushes the opposite skin from the core. Rigid foams will demonstrate different failure modes, such as diagonal core ruptures or delaminations starting in the zone under the point of impact, where the core is crushed but the skin recovers. These are all forms of brittle failure. Since balsa- and rigid foam-cored sandwiches are very resonant, they have, in some cases, demonstrated catastrophic failure when subjected to operating conditions at their natural harmonic.
Sandwich core structures made with thin, high-strength skins and polypropylene honeycomb core also demonstrate the desirable acoustic property of “constrained layer damping.” All materials have a “natural harmonic” or a frequency at which they will sympathetically vibrate. Polypropylene’s “natural harmonic” is at a very low frequency of 125 to 150 Hz. The normal “problem hearing range” is 1,000 to 3,000 Hz. Therefore, the material’s natural harmonic is far below the “problem hearing range.” The nature of sound is that the lower the frequency, the greater amount of energy is required for the sound to be heard. To quantify the difference, the amount of energy required for a 50-Hz noise to be noticed is 1 million times that required for a 3000-Hz noise. This constrained layer damping serves to limit the conduction of structure-borne sound in applications such as bulkheads, decks and stringer systems in boats, automobile load floors, sound enclosures and speaker cabinets, etc.
HoneyComb
To prevent conduction of sound from one side to the other in most single-wall applications, either the wall has to have a lot of mass or substantial absorbers need to be added on the surface. (Sound transmission straight through a wall is referred to as “airborne” sound, even when a wall separates, for example, two rooms otherwise completely sealed off from one another.) Bulkheads designed with CarbonCore Plastic Honeycomb successfully reduce the sound transmission through damping, where other, heavier construction materials may resonate sympathetically and pass the sound on to the other side. By thermo-fusing polyester based scrim cloth with polypropylene-based barrier film underlayment, CarbonCore Plastic Honeycomb provides a 100 percent bonding surface compatible with most resin systems. The dead air space inside the cells provides insulation (an R factor of 3.3 per inch of thickness) not unlike the double-pane windows in a modern dwelling. While most cores excel in providing one or two desirable properties, only CarbonCore DYNAMIC IMPACT RESISTANCE TECHNOLOGY is designed to provide all of them – insulation, stiffness, chemical resistance, toughness and light weight -with the added bonus of sound absorption.
Light. Tough. Quiet.
CarbonCore doesn’t just look good on the lab charts, it stands up to the tests of the real world. The wonderful thing about laboratories is that highly skilled technicians can control the results, but out on the water, bumps and grinds are accidental.
Building with CarbonCore Plastic Honeycomb assures you that your boat is built with material ready to handle all kinds of stresses.
IMPACT STRENGTH
A sandwich construction using CarbonCore Plastic Honeycomb core, with its high degree of resiliency, is more impact-resistant than a singe-skin laminate of equal or higher weight. The increase in impact strength compared to a single-skin laminate is best understood by considering the core as a shock absorber that permits large, distributed deflections of the impacted skin, absorbing much of the energy and therefore protecting the second skin. The basic principle of energy absorption is to take the kinetic energy of a moving object and convert it into internal work. Honeycombs crush uniformly at a known load, have a long stroke and have the highest strength-to-weight ratio of all energy-absorbing materials. They also are very predictable.
At the same time, the core has elasticity sufficient to maintain the bond line between the core and the skins, and is resilient enough to fully rebound when the skin has not been fractured. If the impacted skin is breached, the second skin is most often unharmed, thereby simplifying repairs considerably. Although HoneyCombsandwich construction is not completely puncture-proof, experience shows that its puncture-resistance is significantly better than solid laminate construction when high-elongation core materials are used.
Conversely, sandwich panels fabricated with stiffer core materials will transfer impact and vibration energy from the side of the impact (or outside skin) to the inside skin, thus subjecting the inside skin to face buckling, delamination or catastrophic failure.
VIBRATION DAMPING/SOUND ATTENUATION
With its natural harmonic of 125 to 150 Hz, polypropylene is known for its excellent vibration damping/noise absorption properties. Almost all of our customers who have switched to CarbonCore Plastic Honeycomb from a different core material have reported noticing that boats are quieter. Noise and vibration travel well through a single-skin laminate, but boats with cored hulls are simply quieter. While balsawood and brittle foams in cored hulls tend to transfer noise energy directly through the laminate, polypropylene and some of the more elastic foams further dampen the noise energy due to their elastic nature.
THERMAL INSULATION
A vessel’s thermal insulation is a key consideration since a boat most often sits in water much colder than the ambient temperature. Condensation forms, staining the vessel and creating an environment which promotes the growth of mildew. Sandwich construction significantly aids in the elimination of condensation and associated bilge water. The cored insulating layer coincidentally eliminates the need for highly flammable spray-in polyurethane.
DISPLACEMENT BOATS
Since weight is not the primary concern in displacement and commercial boats, there seems to be a general misconception that these vessels must be constructed with solid laminates. One should not, however, confuse solid with tough and strong. Properly designed sandwich construction has greater impact strength when compared to a single-skin (solid) laminate. Therefore, we believe that sandwich construction is beneficial to the general safety of displacement vessels. The arguments for using composite sandwich construction are overwhelming. No good reason exists for using single-skin fiberglass construction that cannot be countered with a better reason to use a tough, resilient core material like CarbonCore Plastic Honeycombs.
SHEAR PROPERTIES
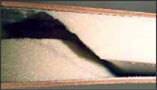
Typical shear failure shown with foam cored sandwich panel
One of the input factors used to determine sandwich laminate thickness is shear strength. Laboratory tests of shear properties, however, do not do justice to some materials, especially honeycomb. Since ASTM and ISO test standards for shear strength specify the sample size – essentially a thin strip of material that is loaded on a relatively short span and measured – honeycomb structures are at a disadvantage because in thin strips, the cell structure is broken along the edges when the sample coupons are cut from a panel. Furthermore, strength values often are cited without indication of the deflection or elongation. High shear strength may be recorded for low elongations, which may necessitate over-designed skin laminates to assure that small deflections will not induce “core shear failure” and consequently catastrophic structural failure. Conversely, low shear strength may be recorded for high elongations, corresponding to deflections that could not be sustained by other design factors or limitations of the laminates
Typical shear failure shows with foam cored sandwich panels, the material would never fail in shear. Full-scale structures must be evaluated as a whole, with large panel performance and shear elongation as critical considerations. This is particularly true when considering honeycomb sandwich laminates.
In the 1960s and 1970s, many boats were built using an early version of PVC linear foam that possessed comparatively low shear strength. Several of these boats are still in service and, obviously, have been very successful designs. Any presumption that shear strength is the key design parameter, therefore, is simply not true. As an example, many composite professionals may remember building airplane models with balsa before learning about fiberglass, when it was logical to start with a rigid base and laminate. Conversely, to apply high-performance laminates on either side of a compliant material was counter-intuitive. But the current generation of young airplane model builders is actually using fiberglass strapping tape over the surfaces of expanded polypropylene foam. Build time is reduced and, most importantly, the virtually indestructible nature of the resulting structure has provided a far more satisfying product. Likewise, when designing structures using polypropylene honeycombs, one must remember that there is a significant difference in the value of the stress and strain at yield than there is at shear ultimate. Polypropylene honeycomb can stretch and carry loads without failure after the yield point, so the value at ultimate shear is still higher than at yield. It is important to keep in mind that the basis of many design specifications pre-dates the common use of multiaxial stitched reinforcements, which are generally higher in strength, but not as thick, and, therefore, have given up some flexural stiffness. However, when used with sandwich construction to provide the required cross-section for flexural stiffness, multiaxial stitched reinforcements are ideally suited for sandwich construction, achieving further weight reductions compared with previous laminations. Furthermore, since the increased strength of multiaxial stitched reinforcements is achieved at greater strains, Carbon-Core Polypropylene Structural Honeycomb is increasingly selected as the most appropriate core material. A thorough designer must, therefore, consider the most important test for core materials -shear strain (in percent), or shear elongation after the yield point (ISO 1922), which most accurately determines the degree of toughness for a specific core. It is not important whether one uses the shear yield or shear ultimate value in design, what is important is that, based on these figures, appropriate safety factors are built in.
When polypropylene honeycomb is used, one can design much higher on the elastic curve because the factor of safety is in the balance of the elastic range of the curve, and then in shear elongation after yield. We are not saying here that successful designs cannot be made with cross-linked PVC or balsawood, with inherently low shear elongation factors, but simply, the shear stress must be in the lower portion of the curve and not too close to the yield. However, even the balance of the elastic range of the curve is seldom sufficient under severe impacts.
Primary focus should be stiffness, but at the same time there should be an adequate safety margin to fall back on. If the structure is stiff enough, the stresses are usually low, but stiffness without damage tolerance is not a desirable attribute.
Several different sources have been used to obtain criteria for composite boat construction, including adaptations of wood designs with interchangeable single-skin fiberglass equivalent. Several criteria are derived from equivalent designs using metallic materials, primarily aluminum. These criteria seem to work well with some older types of core materials, but are lacking when it comes to NEW core materials such as polypropylene honeycomb, especially when thinner skins are used. The greatest lack is in areas where stresses are applied beyond the normal load range.
Most naval architects have as their primary goal a structure with adequate stiffness, buckling resistance and impact tolerance. All of these criteria are achievable with CarbonCore Plastic Honeycomb.
Our CarbonFoam, CarbonBalsa, and CarbonCore Structural Foam Filled products can be supplied in pre-cut kits.
Our kit department uses state-of-the-art CNC manufacturing technology to provide the most accurate, best fitting core for your application. CarbonCore kits are designed to reduce labor costs, reduce inventory space, eliminate waste and speed up production. All kits are manufactured in-house to customer specifications, packaged in sequential order and numbered for ease of installation. An easy-to-understand schematic is included to help reduce employee training costs. Kits ensure product consistency and quality and save you money.
CarbonCore wet laminated, vacuum-bagged composite panels come in sizes up to to 10 ft by 53 ft, with optional gel coat surface in 40 stock colors. Choice of core: Plastic Honeycombs in various cell sizes, CarbonBalsa, CarbonFoam. Skins include 17-oz or 34-oz woven roving, biaxials, lauan, okoume, high-pressure laminates, metals, wood veneers, marble and other stone, and thermoplastics.
A general overview of various core materials used within the boatbuilding industry follows. Although no core material is the answer to every possible application, this section highlights the various aspects of various widely available core materials.
END-GRAIN BALSAWOOD
End-grain balsa (such as CarbonBalsa) first entered wide use as a core material in the early 1960s when the end-grain configuration was introduced.
Balsawood performs exceptionally well in static laboratory tests. The perpendicular end grains form a structure not unlike a miniature honeycomb, achieving a maximum compressive strength as high as any core material available. The high compression values contribute significantly to the stiffness of balsa-built sandwich panels. In a fire, balsa performs well, since it retains its structural load-carrying ability as it burns for a much longer period than foams do. While balsawood also exhibits exceptional shear values, the values typically presented are based on laboratory tests featuring a 0.25-inch thick panel, where balsa is at its peak in shear values. Shear values, however, are significantly reduced as panel thickness is increased.
Another weakness of balsa is its lack of impact tolerance. Specifically, its high compression stiffness causes impacts to be readily transmitted from the outside to the inside skin. One result is that the end grains are easily split, thus provoking delamination of the inside skin, which can often go undetected. Condensation can collect in the void created between the inner skin and the core and eventually result in severe water damage to the core itself. Even if the damage remains localized, repeated impact in the same area can eventually result in a catastrophic failure of the sandwich structure. Due to the low elongation of balsa, particular care must be given to the shear transfer bonding layers on each side of the core, ensuring that a low-modulus transition layer is used to “bed” the core. Timing is critical, since the core must be positioned and, preferably, vacuum bagged before this layer cures beyond gel point.
HoneyCombSince balsa is a lightweight, porous wood with low resistance to water vapor and humidity, it is always sensitive to environmental conditions during manufacture and repair of the cored structure, as well as in the structure’s in-service operating environment. Generally, a balsa-cored boat will require more maintenance and care than those with alternative cores.
POLYMER FOAMS
Plastics are divided into two groups: thermoplastics and thermosets. Thermoplastics have long molecular chains that can move relative to each other when heated and stay in their new position when cooled. Therefore, thermoplastics can be repeatedly thermoformed. Notable among their many attributes is particularly high impactresistance. Conversely, thermosets, a category that includes typical laminating resins, are catalyzed to initiate exothermic reactions that cross-link the molecules, transforming liquid resins into solid materials that retain their shapes permanently and cannot be reformed. Thermosets have many positive attributes, including high mechanical properties and temperature resistance, but often suffer from poor fracture toughness.
URETHANE/POLYISOCYANURATE FOAMS
Urethane foams are often mistakenly compared to polyisocyanurate foams, which were developed for residential insulation applications that demand higher fire resistance and low smoke properties. While they possess similar base chemical components, the difference between them is established by the ratio of the two significant constituents of polyol and isocyanate. The ratio is referred to as the index – urethane foam is low index, while polyiso foam is high index. Low index foams are typically produced in a batch process or bun stock, while high index foams may be run on continuous high-speed lines for roofing board, which can be produced at a lower cost. This cost differential can tempt consideration of the polyiso foam as a core material. However, compared to polyurethane foams (e.g, Carbon-Core’s Foamline brand), polyisocyanurate foams are much more friable and can degrade over time, when subjected to dynamic solicitation.
Thermoset polyurethane foams have been widely used in boats and other composite structures since the mid-1960s and, second only to plywood, polyurethane foams have probably been used to build more successful boat transoms than any other core material. To this day, boat transoms remain one of the most suitable applications for high-density polyurethane foam. Polyurethane foams exhibit exceptional chemical (styrene) resistance and heat tolerance (as high as 250°F). They also provide excellent thermal insulation and exhibit mechanical properties that can actually improve with age. Their weaknesses include catastrophic failure under ultimate shear stress at relatively low elongation, which renders the material unsuitable for dynamically loaded structures, such as boat hull sides and decks.
CROSS-LINKED PVC FOAMS
Cross-linked PVC foams are thermosets. Cross-linked foams have anchor points between molecular chains, which result in higher stiffness, but less toughness. Because of their cross-linked structure, thermosets normally have a higher heat distortion temperature than thermoplastics.
Thermoplastics and thermosets can, however, be blended, creating molecular strings that can be anchored to a certain degree yet take on a degree of thermoplastic toughness as well. When thermoset resins (usually di-isocyanate) are blended into PVC resins, a foam with increased mechanical properties – higher heat distortion properties, and better solvent resistance – is created. However, the resulting foam products have their shortcomings: Elongation of these cross-linked foams is typically much lower than for linear foams. The relative brittleness lowers the foam’s impact resistance and they can shear easily under impact. Cross-linked PVC foams also may be softened or damaged during the molding process by the combination of styrene vapors and heat from the exotherm associated with curing polyester resins. Several cross-linked PVC manufacturers are adding plasticizers to the resin blend, which may cause future problems since plasticizers tend to migrate out of the foam over time, leaving behind an effectively different foam than the structure was originally engineered around. Out-gassing is another problem with crosslinked PVC foams. Cross-linked PVC foams are manufactured in a water steam chamber, because the di-isocyanate component in the PVC needs a water molecule for the chemical reaction (generally described as water-blown in contrast to CFC-blown). Lower density foams are stored for short periods in a temperature- and humiditycontrolled environment for aging. Higher density foams require more time for cure/polymerization. While fully cured PVC foam does not normally out-gas, the phenomenon can occur when the foam is heated and carbon dioxide (CO2) forms within the foam. When the CO2 tries to force its way out of the foam, it tends to push the outside skin away. Since PVC foams are noted for their low heat tolerance, out-gassing can become a significant problem when dark colored laminates are used.
LINEAR PVC FOAM
Linear PVC foams have been successfully used in various forms since the mid-1950s. Even when linear PVC foams exhibit lower mechanical properties than cross-linked PVCs, linear PVC foams in real-life situations still offer one of the highest levels of foam core damage tolerance and toughness, making it ideally suited to boat hull construction, where repeated impacts are a part of normal operation. It is well-suited for dynamically loaded structures, since ultimate failure occurs at very high strain.
The resistance to chemicals (styrene) is limited, so one must be very careful to implement proper shop procedures and use proper resins/adhesives. Amajor drawback to linear PVC foams is the material’s inherent lack of temperature tolerance, making it unsuitable for marine superstructure construction where mechanical properties can suffer from repeated heat cycles endured in marine environments.
SAN FOAM
SAN (Styrene-AcryloNitrile) thermoplastic resin-based linear foams have been successfully used in composite sandwich construction. Typically, SAN foams exhibit higher mechanical properties than equivalent densities of PVC and urethane foams, although they do so at a much higher cost. SAN foams exhibit good toughness characteristics; however, as with all foams, the failure mode when reaching ultimate stress is catastrophic, resulting in a 45° degree crack that can propagate easily as the sandwich panel continues to flex.
HONEYCOMBS
Paper Honeycomb
Paper honeycomb is widely used in the composites industry, mainly due to its low cost, but it is impractical to use material so susceptible to post-damage degradation in marine or outdoor environments. Paper honeycombs, especially in untreated form, are better left to the packaging industry.
Aluminum Honeycomb
Aluminum honeycomb is typically used in aerospace structures, but is unsuitable in most marine-related applications due to poor corrosion resistance as well as high thermal conductivity (no insulation value). Another problem is that the aluminum honeycomb bond line is limited to a very small surface area of the thin cell wall. A small resin ring has to form around each cell to “grab” the core and create the bond to the skin. This is achieved with adhesive films in the aerospace industry. Aluminum honeycombs are used extensively in the aircraft industry, primarily because there are few foams that can withstand the extreme processing temperatures typically required to produce parts for the aerospace sector.
Polypropylene Structural Honeycomb
Polypropylene is noted for its inherent toughness, extreme chemical resistance and elongation. Water or chemical agents used in the composites industry do not affect it. CarbonCore polypropylene honeycomb incorporates a thermo-fused (not glued) scrim, thus providing a 100 percent bonding surface (compatible with most resin systems) for stress transfer between the honeycomb and skins. A barrier film also is incorporated to prevent resin from filling the cell structure.
Some honeycombs have different mechanical property values for length and width directions, due to the fact that the core is weaker along the glue line. Extruded honeycombs (like CarbonCore Plastic Honeycomb) have equal properties in both directions since they are not glued like traditional honeycombs. Carbon-Core polypropylene honeycombs can easily be thermoformed or vacuum bagged in place (unlike foams), without the need for scoring in many instances. Elimination of scoring can prevent excessive resin uptake and the associated cosmetic or structural defects.
The mechanical properties of CarbonCore Plastic Honeycomb are controlled by the following specifications: 1) physical properties of the thermoplastic; 2) cell diameter; 3) wall gauge (thickness of the cell wall); 4) core thickness; and 5) facings applied to the core. Altering one or more of these specifications will produce different performance characteristics. CarbonCore honeycombs can be engineered to be a specific weight, absorb a specific load, rebound at a specified rate and possess the flexibility or stiffness required by the end application.
HONEYCOMB SUMMARY
In short, many claims and counter-claims may be made about which product has the best properties for a given application. The structural properties that you actually achieve are very dependent on the manufacturing process. You must design structures with physical properties based on real values that the shop can consistently produce. With elongation exceeding that of any other type of core material, CarbonCore Plastic Honeycomb is the toughest, most resilient core available. Under stresses beyond its design loads
A Carbon-Core installation, using vacuum bagging, is shown. Note the alternative core used as a perimeter enclosure for edging purposes. This method retains the sound-damping qualities of the part.
It deforms and stretches; however, it remains intact and, unlike with foams, stress cracks do not travel, but remain localized for easy repair. Polypropylene honeycombs remain a viable core of choice for superstructures, floors, bulkheads, stringers and hull sides as well as numerous small composite parts and structures.
It is difficult to compare core materials using only the mechanical data. As noted previously, many other properties must be considered to properly evaluate the overall situation. While some core materials have certain properties that are exemplary, one shouldn’t look at these isolated properties without taking into account other aspects, including cost. While most cores provide one or two desirable properties, only CarbonCore DYNAMIC IMPACT RESISTANCE TECHNOLOGY is designed to provide them all – insulation, stiffness, chemical resistance, toughness and light weight and sound absorption
Fully considered, nothing available provides the cost/performance benefits of DYNAMIC IMPACT RESISTANCE TECHNOLOGY from CarbonCore.
Download our PDF brochure on CarbonCore Dynamic Impact Resistance Technology.
Thanks to its physical and chemical properties, polypropylene is resistant to water and will not absorb it. Thus, CarbonCore honeycomb materials are ideal for numerous areas of industry such as:
- Boat-construction: hull, deck, flybridge, sole, door, stringer, hatch, interior. Thousands of boats are built every year using CarbonCore Structural Honeycomb. CarbonCore’s tough and rot-proof core will result in stronger and more durable structural boat parts; in addition, as compared to foam, balsa wood, or paper honeycomb, the boat became much quieter than before due to its inherent best in the business sound and vibration dampening qualities.
- Equipment specific to marine construction, such as floating docks.
- Swimming pool construction, either for the swimming pool itself (used for this purpose, our honeycomb materials add thermal insulation characteristics to maintain the water temperature) or for accessory elements like staircases or annex premises.
- Features connected with sanitary arrangements, like shower tubs or bathroom fittings in general; in this case honeycomb materials can be used with polyester skins or Formica as well as with marble or many other types of solid surface skins.
- Fish farm filtration ( using 24″ thick CarbonCore unscrimmed blocks)